SCADAにDCSにPLC ……それぞれ機能が似ており違いを明確に説明しづらくなっています。
DCSやPLCは現場機器であるセンサーやアクチュエーターと接続してプログラム通りに制御を実行します。
対してSCADAは複数あるDCSやPLCなど制御機器を集約して監視・指示する役割があります。
役割から見た違い
まずはそれぞれの基本的な意味と役割を押さえ比較します。
理解しやすいようにタイトルとは違う順序で取り上げています。
PLCとは
PLCはProgrammable Logic Controllerの略で、主にファクトリーオートメーション(FA)分野で使用される制御実行機器です。
数ミリ秒程度の周期で信号を読み込むものも多く、正確さや複雑さを求められる様々な産業機械で採用されています。
安価で拡張性が高いことから、バッチ製造や連続製造のプロセスプラントでも小規模であればPLCが積極的に採用されます。
また後述するPLC計装を活用することで中規模のプラントでも十分に制御できる能力が備わっています。
DCSとは
DCSはDistributed Control Systemの略で、主にプロセスオートメーション(PA)分野で使用される制御実行機器です。
石油精製プラントや発電所など大規模設備でも使用されています。
PLCと比べてバルブやポンプなどの制御が主目的であり、1秒程度の周期で信号を読み込みのが一般的です。
名前の由来は制御ユニットを系統ごとに分散配置していることから来ています。
大規模システムが”止まらない”、異常が周りに”波及しない”ことが売りの長期継続運転に適した制御システムです。
ただしメーカー独自色が強く、初期費用・維持費用は共に高い点が問題となっています。
DCSに関しては以下の記事で詳しく解説しています。
SCADAとは
SCADA(スキャダ)はSupervisory Control And Data Acquisitionの略で、プロセス制御の集中監視と指示を行います。
つまり複数のDCSやPLCを一括監視する役割があります。
監視用グラフィック画面のみならずアラームやレポート、ロギング、トレンドなど監視に使う様々な機能が備わっています。
SCADAとDCSの違い
DCSの多くは構成要素として指示監視機能が備わっており、少しSCADAと似ています。
SCADAは全体を集中監視するのに対し、DCSは自身の制御に関係する機器のみを監視しています。
つまり系統ごとにDCSの監視機能は分散して設けられており、それらを1つに集約して監視しているのがSCADAです。
そのため単一施設でDCSのみでも問題なく監視できているところに敢えてSCADAを導入する必要はありません。
更に言えば、機能向上に伴いSCADAを用いなくともタッチパネルとPLCのみで制御システムが完結する例も増加しています。
システム階層から見た違い
SCADA、DCS、PLCそれぞれの役割が分かりましたので、次は製造システム全体で見た位置付けから比較します。
また関係するMESやBIなどとの違いも解説します。
参考とする規格ISA-95
製造システム全体を分かりやすく階層に分けて整理されたISA-95という規格があります。
ISAは自動機器に関する国際的な標準化団体です。
ISA-95は製造システムと経営システムを円滑に連携するために策定されました。
今回はこちらの規格を参考にSCADA、DCS、PLCの位置付けを確認します。
参考資料:製造オペレーションマネジメント入門~ISA-95が製造業を変える~
SCADA、DCS、PLCの階層
イメージしやすいようISA-95を参考に更に細分化して階層分けしてみました。
※正式にはSCADAやDCS、PLCは制御系として、ERPやBIは経営系として1つにまとめられ4層構造になっています。
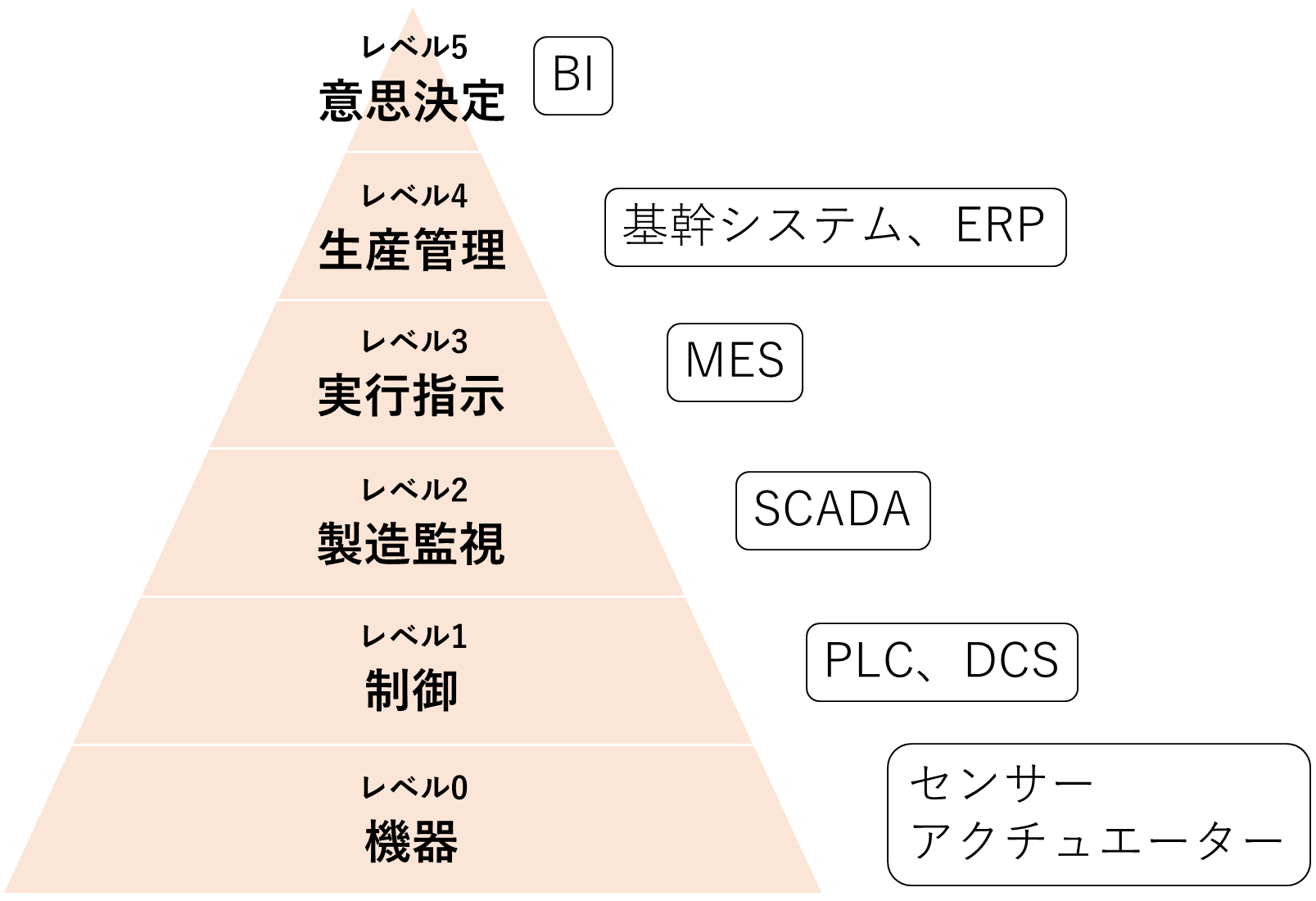
SCADAやDCS、PLCどれも経営側というよりも現場側である下位層に位置しています。
本記事では具体的に述べませんが、DXが進むにつれて上位システムとの円滑な連携が重要視されます。
関係する技術の一つとしてOPC UAが挙げられます。
MESとの違い
MESは製造実行システムとも呼ばれるスケジューリングや工程管理を行うシステムです。
SCADAよりも1つ上位の層です。
MESは社内の販売計画を基に工場でどのような段取り・人繰りで製造するか詳細を管理しSCADAやDCS、PLCなど下位層へ指示します。
MESで管理、SCADAで監視、DCSやPLCで実行するイメージです。
BIとの違い
BIはビジネスインテリジェンスの略で、企業の様々データを可視化・分析するためのツールです。
ビッグデータと呼ばれる膨大なデータを整理でき、特に経営における意思決定に使用されます。
可視化して判断するためのツールですのでSCADAと混同しそうになりますが目的が全く違います。
BIツールから決定した販売計画をMESに落とし込み具体的な製造計画が立てられます。
そのためMESやSCADAよりも更に上位の層で、最上位にあると言っても過言ではありません。
PLC計装(DCS代替)
DCSはメーカー依存が激しいことにより高い初期費用・維持費用が問題となっています。
そのためDCSの機能をPLCで再現したPLC計装を採用するところが増えています。
DCSが流行った数10年前ではPLCのCPUの性能も悪く、大量のループ制御を行うプラントには向きませんでした。
現在ではCPUの処理性能が向上したおかげでDCSのような使い方ができるようになりました。
今や電源やCPU、ケーブルまでも二重化できるシステムになっています。
設備構成
制御ユニットとして多くは二重化対応したPLCが用いられます。
さらに指示監視の役割でSCADAと組み合わせて使用します。
各機器間はEthernet、特に産業用Ethernetで接続して信頼性の高い制御を実現します。
どのように使い分けるのか
普段の取り回しの良さを考えると、個人的にはDCSの必要性が無い限りPLC計装で良いと思っています。
ただしPLC計装はあくまでDCSの特徴に似せた製品であるだけです。
横河電機の技術情報誌ではDCSについて「24 時間 /365 日の連続使用という条件での高い稼働持続性が要求される」と表現するなど連続稼働に対する強い意思表示をしています。
なんとコアとなる制御システムの稼働率は99.99999%(セブンナイン)以上とのことです。
これは待機側CPUを設けるだけでなくメイン・待機ユニット内にもそれぞれ照合用CPUを設ける「ペア&スペア方式」のような独自技術が取り入れられているためです。
入出力点数やループ制御点数といった制約を除けばDCSを選択する明確な基準はありません。
安全性や経済的・社会的影響を加味し、何が何でも止めてはいけない!というような場所ではDCSを選択すべきです。
PC制御
最後は少しおまけの要素、PC制御です。
正直なところプロセス業界において導入実績を聞いたことはありませんが、今後普及する可能性があるため取り上げました。
DCSやPLCのような制御ユニットが産業用PCに置き換わっています。
DCSやSCADAでも監視のために産業用PCが使用されますが、制御機能全体にPCを採用しているところが特徴的です。
特にIT領域との連携やAI系高度システム導入など、従来追加ユニットを設けて実現していた機能をPC内で容易に完結するのに向いていると考えられます。
ベッコフオートメーションではプロセス産業向けソリューションも展開されておりイメージしやすくなっています。
TwinCATというソフトウェアがPC制御の鍵でPLC言語でもプログラミングできる仕様です。
オススメ書籍
・図解入門ビジネス工場・プラントのサイバー攻撃への対策と課題がよ~くわかる本
制御システムの基本構成に始まり、セキュリティの基礎を理解することができます。
今後はプラントも外部と繋がっていく時代になるためセキュリティ上のリスクを理解するのに最適です。
-
-
図解入門ビジネス工場・プラントのサイバー攻撃への対策と課題がよ~くわかる本
www.amazon.co.jp
・産業用ネットワークの教科書
様々な産業用ネットワークの特徴を1冊にまとめた書籍です。
ネットワーク同士の関係までは記載されていませんが、広い知識を得る点ではオススメできます。
-
-
産業用ネットワークの教科書~IoT時代のものづくりを支えるネットワークと関連技術
www.amazon.co.jp